DOWNTIME in Lean
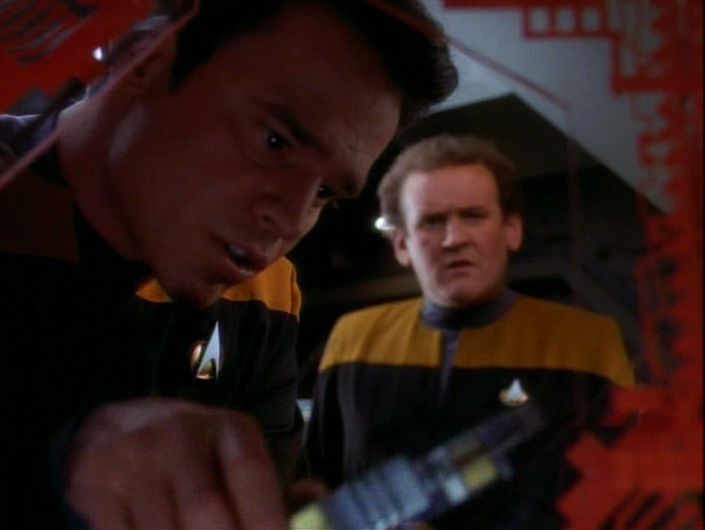
In lean, waste is the enemy. Every bit of wasted time, effort, or resources pulls the company down and impedes its ability to achieve its goals. The eight wastes of lean are: Defects, Overproduction, Waiting, Non-Utilized Talent, Transportation, Inventory, Motion and Processing. The Starfleet Leadership Academy podcast episode DS9: Whispers covers these as well.
1) Defects – the quality of a product that doesn't meet the customer demand or specification. This is measured as Quality Loss and occurs anytime a defective item has to be reworked, repaired, returned or scrapped. DMAIC and DMADV are great methods use to resolve defects depending on how new or established a process is.
2) Overproduction – producing more goods or services than are needed by the customer, done in anticipation of future demand. It creates an excess inventory level which requires storage space and hides defects, resulting in lower quality products. Just-in-time production is one way to combat this loss.
3) Waiting – the amount of time the customer must wait for a product or service. Time losses include delays, equipment breakdowns and delivery shortages. The only way to combat this loss is to offer a better service that can be delivered faster and/or with higher quality, thus creating an improved standard of living.
4) Non-Utilized Talent – the workers' skills and talents that aren't being used to their fullest potential. This is a cardinal waste, in my opinion, because it wastes people. It is often caused by over-production/under-utilization of equipment and inflexible processes, so Lean must address both issues.
5) Transportation – moving materials or products from one location to another, either within a facility or from one facility to the next. Minimizing transportation time is important to reduce costs and improve flow, but it isn't always an easy task because of the unpredictability of product mix and volume, scheduling constraints, etc.
6) Inventory – anything that's produced or bought for future use. There are two types of inventory:
- Excess Inventory – more than what's needed for immediate customer demand, which can delay lead time and require additional space. It also hides defects because the product doesn't move through the system until it's ready for use (think stockrooms).
- Defective Inventory – there are two types of defective inventory: concealed damage (a car with a bent fender) and revealed damage (a car that's been involved in an accident). Just-In-Time is a great countermeasure for this loss.
7) Motion – any physical movement of people, machines or materials. Excessive motion wastes time and contributes to fatigue which tends to lower production quality while increasing worker errors. Lean's tools, such as Kanban and 5S, and my favorite - the spaghetti map, can help reduce this waste.
8) Processing – the time it takes to complete a simple task that does not add value to the product or service. This is where mistake proofing comes into play because by preventing defects you also reduce processing losses.
This list isn't complete and the actual number of wastes will vary depending on who you ask, but this provides an overview.
* source: https://goleansixsigma.com/8-wastes/
This post contains affiliate links. I may receive a commission for purchases made through these links but it won't cost you any more.